Saldatura: saldare l’alluminio con procedimento MIG
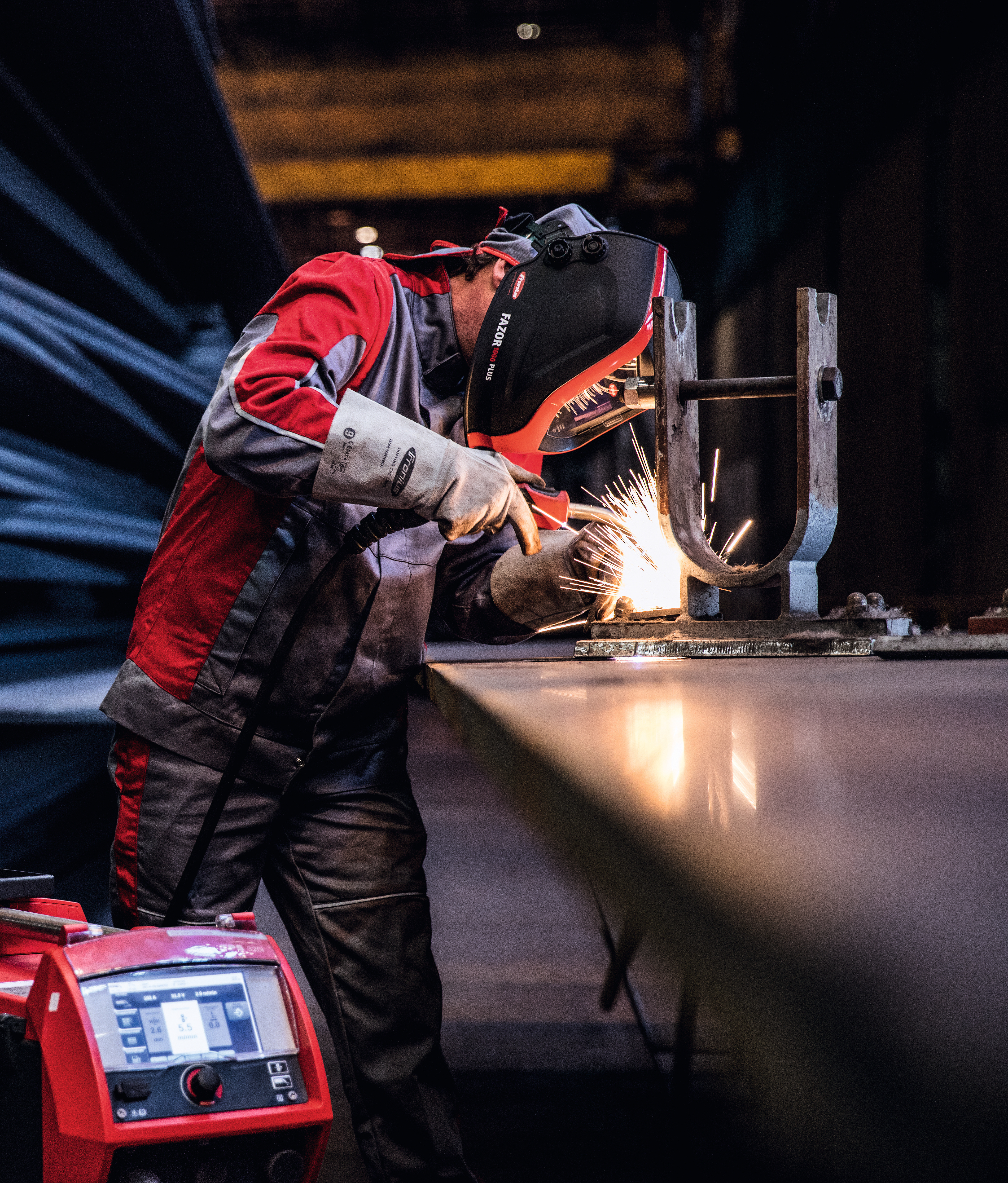
Saldare l’alluminio (Metal Inert Gas, procedimento 131, EN ISO 4063) può essere una sfida anche per un saldatore con una certa esperienza. Ottenere un buon risultato, sia dal punto di vista estetico che funzionale, richiede conoscenze specifiche, accortezze e tecnologie adeguate per eseguire con successo una saldatura di questo particolare materiale.
Vediamo quindi insieme come saldare l’alluminio con procedimento MIG (GMAW - Gas Metal Arc Welding) e a quali aspetti porre attenzione per sfruttare i vantaggi di questo materiale, senza subirne le difficoltà.
Saldare l'alluminio con procedimento MIG
Quando si esegue una saldatura dell'alluminio con procedimento MIG è necessario comprendere alcuni fattori, quali:
- caratteristiche dell'alluminio e leghe di alluminio
- resistenza meccanica
- come si prepara il materiale
- il preriscaldamento del materiale
- gas di protezione utilizzato
- aspetti operativi della saldatura
- come scegliere il generatore
- valutare i possibili difetti dei giunti
- tipi di trattamenti termici applicabili
Analizziamo insieme questi punti.
Alluminio: caratteristiche
L’alluminio è un elemento chimico, in particolare un metallo non ferroso duttile. Leggero e resistente, ha un’elevata conducibilità termica pari a 204 W/m°C ed elettrica e una temperatura di fusione relativamente bassa, circa 660°.
Reagisce con l’ossigeno producendo una pellicola di ossido di alluminio. Proprio questa sua ossidabilità può creare dei problemi durante il processo di saldatura. L’ossido di alluminio, l’allumina, infatti è durissimo e fonde solo ad altissime temperature, circa 2000° C.
Con temperature elevate, inoltre, questo strato di ossido tende ad aumentare in spessore e diventa così sempre più difficile eliminarlo.
Quindi, il processo di rimozione dello strato di ossido deve essere fatto in precedenza, prima della saldatura, per evitare che particelle di ossido rimangano intrappolate nel metallo fuso mettendo a rischio l’integrità del giunto saldato.
L’alluminio è saldabile con tecniche MIG, TIG e saldo brasatura, con l’uso di gas inerti.
Esistono altri procedimenti per poter effettuare giunti saldati su leghe di alluminio che però, a differenza di quelli citati, non utilizzano un arco elettrico.
Le leghe di alluminio
Il mercato offre, a seconda delle necessità operative e dei campi di impiego, diverse leghe di alluminio che sono distinte tra loro attraverso dei codici alfanumerici. L’alluminio è, in effetti, uno degli elementi che più si presta a costituire leghe.
L’alluminio e le sue leghe hanno caratteristiche metallurgiche nettamente diverse da quelle degli acciai. Infatti, anche da un punto di vista normativo vengono trattate separatamente. Abbiamo certificazioni per:
- saldatori (EN ISO 9606-2)
- procedimenti (EN ISO 15614-2)
- livelli di qualità delle imperfezioni (EN ISO 10042) con le relative tre classi di accettabilità
Il sistema di classificazione internazionale prevede 4 cifre e 9 classi in base agli elementi principali che costituiscono le leghe e ai trattamenti subiti.
Ogni classe ha caratteristiche specifiche che dipendono dagli effetti di ogni elemento, per esempio:
- il silicio aumenta la fluidità e riduce il coefficiente di dilatazione (serie 4000)
- il magnesio aumenta la resistenza alla corrosione e la duttilità (serie 5000)
- il manganese aumenta la resistenza meccanica (serie 3000)
- il rame aumenta la resistenza meccanica, soprattutto a caldo (serie 2000)
- il zinco aumenta resistenza e durezza (serie 7000).
La classe 1000 indica l’alluminio puro con un minimo del 99%.
La resistenza meccanica
Anche le caratteristiche di resistenza meccanica distinguono l’alluminio da altri materiali. Si hanno infatti valori con limiti modesti che si attestano in una gamma che varia da 75 N/mm2 a 145 N/mm2, considerando l’alluminio “puro”. Questa caratteristica lo rende poco utilizzato da solo.
Se si considerano le leghe con i relativi trattamenti specifici, i dati relativi alla resistenza meccanica possono variare anche di molto. Basta l’aggiunta di quantità anche piccola di elementi leganti per ottenere leghe leggere con una resistenza meccanica che varia da 650 kg/cm2 a 5.800 kg/cm2 di una lega Alluminio-Zinco, classe 7000.
Preparazione del materiale di base
L’alluminio, per essere lavorato, deve essere sottoposto a delle attività di pulizia iniziale. La fase di pulitura deve precedere quella della saldatura, lo scopo è rimuovere la pellicola di ossido superficiale (allumina) e contemporaneamente eliminare tutte le impurità bassofondenti che si possono trovare sulla superficie.
L’asportazione della pellicola di ossido superficiale è un aspetto molto importante. Infatti questo sottilissimo strato di ossido presenta, come abbiamo visto, delle temperature di fusione molto più elevate del materiale stesso e quindi compromette il regolare svolgimento del processo di saldatura.
Altro aspetto molto importante è quello legato agli eventuali bassofondenti, che sono tutte le impurità superficiali, che vengono definite con questo termine perché presentano delle temperature di fusione molto più basse rispetto al materiale base.
La loro presenza causa una concentrazione nell’asse centrale del giunto saldato. La temperatura di fusione molto più bassa determina un raffreddamento allo stato solido molto più tardivo rispetto al materiale di saldatura depositato. Questo fa sì che gli eventuali bassofondenti si dispongano nella zona centrale, causando una vera e propria linea di fragilità. Qui le tensioni causate dal ciclo termico applicato mediante la saldatura potranno causare una rottura del giunto.
Quindi, rimuovere le impurità e la pellicola di ossido superficiale è determinante per ottenere una buona saldatura.
Per rimuovere la pellicola di ossido superficiale si possono utilizzare spazzole con setole in acciaio inox, solventi o altri mordenti.
È necessario porre attenzione a non spazzolare in modo grossolano. Infatti, uno spazzolamento approssimativo potrebbe fare incorporare maggiormente gli ossidi nel pezzo da saldare. Inoltre, è bene scegliere una spazzola da usare solo per l'alluminio, non vanno utilizzate per l'alluminio le stesse spazzole usate per altri materiali, come l'acciaio o l'acciaio al carbonio, perché risulterebbero inquinate.
Per ridurre al minimo il rischio di contaminazioni, è importante pulire le spazzole con uno sgrassatore. Lo sgrassatore, che non deve contenere idrocarburi, ha anche la funzione di eliminare le parti di bassofondenti quali ad esempio olii, grassi, ecc. provenienti da lavorazioni eseguite in precedenza.
Un altro aspetto importante si può riscontrare nella forma geometrica della preparazione dei lembi delle due parti da unire. Anche per questo esiste una normativa specifica che delinea le modalità e le caratteristiche idonee in conformità con il materiale utilizzato (UNI EN ISO 9692).
Preriscaldo del materiale base
Come abbiamo visto, l’alluminio ha una elevata conducibilità termica, circa 2,5 volte maggiore rispetto a quella degli acciai al carbonio o delle leghe di nichel.
Questa comporta un notevole assorbimento di calore da parte del materiale, con il rischio di deformazione dei pezzi. Inoltre, per evitare fusioni parziali o incollature, cioè la mancata fusione, si dovrebbe usare un forte apporto di calore, ma questo, di contro, potrebbe addirittura sfondare il giunto, perché l’area interessata alla fusione tende ad allargarsi rapidamente per via della conducibilità termica.
Per questi motivi, prima di procedere con la saldatura dell’alluminio, per alcuni spessori, che a causa della loro massa comporterebbero una elevata e repentina dispersione di calore, è necessario preriscaldare i pezzi.
Un altro vantaggio del preriscaldo è la possibilità di usare parametri con apporti termici più contenuti e creare quindi un ciclo termico generale del processo meno severo.
La temperatura di preriscaldo non dovrebbe superare i 110°C. Per rilevare la temperatura ed evitare un sovra riscaldamento, si consiglia l’utilizzo di termometri, marcatori con sfera, marcatori lunga durata con essiccazione rapida, matite termiche.
In merito a eventuali termometri da utilizzare, con l’alluminio i più indicati sono i dispositivi con sonda a contatto, perché risultano essere più precisi.
I misuratori laser, pur essendo di largo utilizzo per altri tipi di materiali, presentano delle difficoltà e inesattezze nei valori di temperatura rilevata quando sono utilizzati sull’alluminio. La sua superficie semi lucida può contrastare la risposta effettiva del laser e dare misurazioni con indice di inesattezza anche consistente.
Gas di protezione
Il gas più comunemente usato nella saldatura dell’alluminio e delle sue leghe è sicuramente l’argon puro.
Si possono utilizzare anche miscele di gas che sono facilmente reperibili in commercio, per esempio argon-elio. Queste miscele di gas hanno tutte, naturalmente, la caratteristica di essere inerti.
Infatti, il gas ha la funzione di impedire all’aria di ossidare il metallo e porta a un aumento delle temperature dell’arco elettrico, migliorando la fusione del materiale stesso.
Proprio per questo aspetto, le miscele sono solitamente impiegate per applicazioni manuali dove ci siano in gioco spessori consistenti oppure per applicazioni automatizzate, con correnti di saldatura e velocità di saldatura maggiori, in quanto si possono ottenere risultati migliorativi anche in termini di tempistiche di produzione.
Saldatura: aspetti operativi
L’alluminio, avendo un’elevata conducibilità termica, impone l’uso di correnti più elevate e maggiore velocità di avanzamento.
Se la velocità è troppo ridotta si rischia lo sfondamento del materiale base, viceversa, se la velocità di avanzamento risulta essere troppo elevata in rapporto ai parametri impostati si possono verificare due casi.
Il primo che la velocità di dissipazione del calore del materiale provochi delle incollature o addirittura delle mancate fusioni.
Il secondo caso che si possano facilmente riscontrare delle porosità incluse nel bagno di saldatura. Questo fenomeno è dovuto alla mancanza di un adeguato tempo di solidificazione del bagno che non permetterebbe la fuoriuscita dei gas che si sprigionano durante il processo.
Generatori
Nello scegliere il generatore per la saldatura dell’alluminio, prima di tutto bisogna decidere la modalità di trasferimento, spray-arc o pulsato.
Lo spray-arc prevede un trasferimento di metallo fuso sotto forma di un flusso di goccioline continue. Un esempio di applicazione di questa modalità di trasferimento si può riscontrare in applicazioni su elevati spessori di alluminio, che richiedono correnti superiori ai 350 A.
Un’altra possibilità viene data dall’utilizzo di trasferimenti di tipo pulsato, ottenuto con i generatori a Inverter. I generatori di nuova generazione sono dotati di programmi dedicati ai vari tipi di leghe e differenziati in base ai diametri del filo utilizzato durante la saldatura.
Durante la saldatura MIG ad arco pulsato, a ogni pulsazione, una gocciolina di materiale d’apporto (filo) viene trasferita al materiale base in modalità controllata in merito a dimensioni, velocità di creazione, temperatura, creando di conseguenza la saldatura del giunto.
Questo procedimento consente di ottenere una saldatura con meno spruzzi, una diluizione e regolarità di superficie migliore.
Saldatrice Fronius multiprocesso MIG / MAG, TIG, MMA TransSteel Compatta
Il procedimento MIG pulsato sull'alluminio consente un migliore controllo dell'apporto termico, dà la possibilità inoltre di effettuare saldature fuori posizione e di saldare anche spessori molto sottili a basse correnti.
Vanno inoltre considerati aspetti come ad esempio lo scorrimento del filo, che nella saldatura MIG può essere difficoltoso perché il filo è più tenero dell'acciaio e tende ad aggrovigliarsi nei rullini.
Per questo i generatori dovranno essere corredati di accessori idonei. Per esempio i rullini trainafilo dovranno essere specifici per l'alluminio e andrà impostata una pressione adatta sul filo. Infatti, una pressione eccessiva può deformare il filo e causare una alimentazione irregolare; una pressione troppo bassa può al contrario non essere sufficiente e causare uno scivolamento e una incostanza nell’uscita del filo.
Va predisposta una torcia specifica per l'alluminio, meglio se modello push pull con motore incorporato. Questo aiuterà la fuoriuscita del filo costante e controllata.
Le guaine specifiche in grafite o teflon garantiscono un perfetto scorrimento, mentre sono sconsigliate le guaine tradizionali in ferro.
Possibili difetti dei giunti saldati
L’alluminio presenta delle possibilità di difetti nei giunti saldati proprio a causa della sua natura metallurgica e delle sue caratteristiche.
Porosità e incollature risultano essere i tipi di difetti più facilmente riscontrabili in un giunto saldato.
Altro aspetto importante si può riscontrare nella modifica che subisce il materiale base nella zona adiacente la saldatura. La modifica può consistere in una perdita della resistenza meccanica di modesta entità se il processo, nella sua globalità, è stato eseguito rispettando i dovuti standard, oppure considerevole in caso contrario. Questo aspetto viene definito tecnicamente softening.
È dovuto al ciclo termico e all’apporto termico che scaturisce dal processo di saldatura. Per questo è necessario ridurre i difetti causati dall’input termico con la corretta impostazione del processo e l’utilizzo di idonee attrezzature.
Trattamenti termici
In merito ad eventuali trattamenti termici applicabili a questo tipo di materiale base, si possono evidenziare principalmente quattro tipologie:
- trattamento termico di solubilizzazione
- trattamento termico di invecchiamento
- trattamento termico di ricottura
- trattamento di incrudimento mediante lavorazione plastica
Questi trattamenti danno origine a degli stati metallurgici diversi tra loro che hanno caratteristiche differenti rispetto al materiale base.
La scelta del trattamento termico va quindi effettuata considerando vari aspetti, per esempio le lavorazioni a cui sarà sottoposto il materiale base e i campi di impiego della struttura realizzata.
Ottimizza oggi la tua saldatura dell'alluminio con i migliori generatori MIG e accessori specifici. I nostri esperti sono pronti ad analizzare le tue esigenze.
Pronto a saldare l’alluminio?
In conclusione, l’alluminio, per le sue caratteristiche specifiche, può essere usato con grande vantaggio in molti settori applicativi. D’altra parte, proprio le sue specifiche caratteristiche possono rendere difficoltoso il processo di saldatura.
Solo un’attenta valutazione dei pro e dei contro possono farci decidere i materiali e i procedimenti migliori da utilizzare.
Un ambiente adatto, la strumentazione adeguata, le protezioni corrette sono il minimo per partire. Le tecniche, invece, si imparano e si affinano con l’esperienza.
Se hai domande o necessiti di consulenza da parte di un esperto per ottimizzare il processo di saldatura dell'alluminio, contattaci oggi stesso.
Siamo qui per fornirti supporto professionale e aiutarti a superare le sfide legate a questo metallo versatile.
Hai bisogno di supporto per la tua prossima saldatura di alluminio? Parla con un nostro esperto oggi stesso.